From Hype To Bust and Back Again
Additive Manufacturing, also known as ‘3D Printing’, has been an ongoing technological revolution for many years now. However, it disappointed its early supporters, who expected it to replace traditional manufacturing completely.
This misjudgment can be explained by the “hype cycle” almost always driving the adoption of new technologies. It essentially goes this way:
- A rising phase, where the exponential growth of tech capabilities makes everything seem possible.
- A downtrend phase, where reality and real-life limitations become apparent, making the previous hype appear as “just a fade.”
- A slower, but more sustainable rise back of the technology, with maturing of the industry and expanding adoption by more users over time.
This cycle was very much at play with 3D printing. What made it even more complex is that 3D printing can be done with many materials and for many applications, meaning that different sub-sections of additive manufacturing are located at different points of the hype cycle.
In 2018, the Gartner expert consulting company published a snapshot of the 3D printing industry at the time.
Source: Fabbaloo
In hindsight, this was a pretty accurate view. Many 3D printing technologies are going through or finishing the “trough of disillusionment.” This is especially true for potentially world-changing techs like organ 3D printing or domestic 3D printing.
At the same time, the applications that had already entered the consolidation phases, like prototyping or dental implants, now form the core revenues of most 3D printing companies.
Consolidation Before Further Expansion
The “trough of disillusionment” is a period marked by a loss of interest in the technology that has “disappointed” investors. As a result, funding can be hard to find, and unprofitable companies tend to be absorbed by better-funded ones.
This effect has recently been in full effect in the 3D printing industry. The latest consequence was the purchase of Desktop Metal by Nano Dimension for an all-cash transaction of $185M-$135M.
This news came on top of regular and messy tentative consolidation in the industry, notably with Stratasys being courted during all of 2023 for merger or acquisition by all its 3 large competitors 3D Systems, Desktop Metal, and Nano Dimension.
The failed and successful acquisitions of 2023-2024 were themselves the results of a previous wave in 2022, with no less than 22 acquisitions of smaller 3D firms by its competitors in that year alone.
It seems that 3D printing will soon quickly consolidate into a market with a few leaders gathering together the key IPs and reaching the scale needed for profitability.
It is typically after such consolidation that an innovative industry exits the “trough of disillusionment” and enters a durable growth phase that can last many years or even decades.
So, it is worth looking at where the additive manufacturing industry is standing today, and where it will go from here.
How Does It Work?
At its most basic, a 3D printer brings the intended material (in this case, plastic, in the shape of a long filament) to a nozzle, where it is melted and extruded on a print bed.
The nozzle keeps moving following a computer’s instruction, slowly applying the material to form the intended shape. Multiple layers allow for the object to take its 3D shape over time.

Source: ResearchGate
Earlier or cheaper generations of 3D printing had a fairly rough look, with each layer very visible.

Source: ResearchGate
Over time, progress in nozzle technology, filament quality, and curing of the material created a lot smoother aspects both more functional and more aesthetically pleasant.
In addition, many systems require extensive “support structures” to hold the freshly printed material in place until it solidifies. This can cause the design of the 3D model to be more complex, especially if the goal is to reduce the possible support structure to the minimum in order to avoid wasting too much material.

Source: 3D Sculplab
More advanced systems, notably with nozzles capable of movements with 6 degrees of freedom or immediate UV exposure to speed up curing/solidification, can reduce or remove the need for support structures.
Limited Initial Markets
3D printing was initially conceived with plastic (and later resins) to produce molds and parts directly from digital 3D files without the steps required by traditional manufacturing. This was an immediate hit for the nascent additive manufacturing technology, as it bypassed the need for complex and expensive molds to produce uniquely shaped plastic pieces.

Source: Form Labs
This opened a few markets to the industry:
- Prototyping, as well as quick production and testing, can speed up the development process and save money.
- On-demand production is needed for maintenance and repair of rare parts or for urgent needs.
- Hobby production, with no intention of ever doing later mass manufacturing.
These were however somewhat limited markets, in comparison to the astonishingly large revenues of the manufacturing industry of $13.5T, or 16.6% of total GDP.
This makes the current $20B 3D printing market and the $500B forecast for 2030 by ARK Invest much less outstanding, as it would imply that a mere 3.7% of global manufacturing move on from traditional methods to 3D printing.
Many Plastics Options
Still, each of these markets supported the development and maturation of this first generation of 3D printers. Progressively, more advanced printing techniques appeared, and more types of plastic and resins became available.
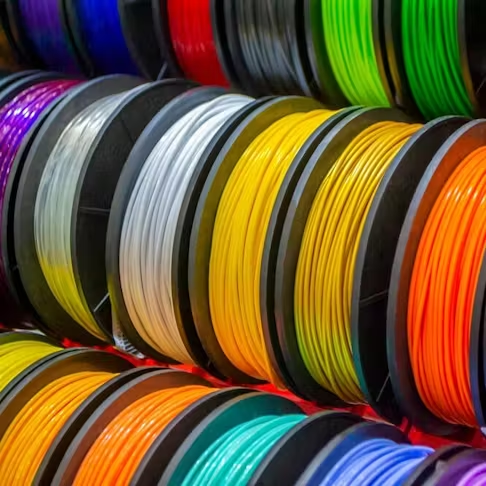
Source: Xometry
This includes:
- Acrylonitrile Butadiene Styrene, or ABS, the material used to make Lego bricks, as well as car parts.
- Polylactic acid, or PLA, a biodegradable plastic made from renewable corn starch.
- Acrylonitrile styrene acrylate, or ASA, similar to ABS but with a better resistance to UVs, making it better suited to applications exposed to sunlight.
- Polyethylene terephthalate, or PET, the plastic used to make bottles and is generally best used for anything that touches food.
- Polycarbonate, or PC, used in greenhouses for example, mostly valued for its strength and transparency.
- Polypropylene, or PP, known for its flexibility and resistance to wear, making it widely used in the automotive and textile industry.
- High-Performance Plastics: Polyether ether ketone (PEEK), polyether ketone ketone (PEKK), and Polyetherimide (ULTEM®). These plastics have mechanical properties similar to metal while being significantly lighter. This makes them attractive for the automotive, aerospace, and medical industries.
- Many more types of plastics, including polyamides (like nylon), polymer blends (mixing different plastics in the same filament), high-impact polystyrene (HIPS), polyvinyl alcohol (PVA), etc.
From Plastic To All Materials
For a long time, the discussion around 3D printing was centered around improving the efficiency and diversity of usable plastics. The need for biodegradable plastics is also shared with the traditional plastic manufacturing industry.
This changed over time as more companies looked at additive manufacturing and realized they could apply its key principles to many other materials.
3D Printing Metals
Plastics are everywhere in the items we use. However, the use of 3D printing in the plastic industry hit the limit that most plastic items are made to be cheap and mass manufactured, with a usually simple design.
For this usage, the heavy investment in molds and automation makes sense, as millions of plastic pieces will be created. In contrast, 3D printing might forever be a little slower and more expensive on a per-unit basis.
However, metals are much more robust and have unique characteristics like high-temperature resistance, conductivity, etc.
Metals require often complex and expensive forging, stamping, and milling to achieve a desirable form. And no matter what, these methods put strong constraints on the achievable design. As a result, a lot of different parts and complex assembling is often required for items made of metal.
3D printing metal was first developed by using metal powder, which is deposited and then melted by a laser. This is the base for the two most used metal 3D printing methods:
- Selective Laser Melting (SLM), where the metal powder has a single melting point and the laser melts all the metal powder.
- SLM produces parts in a single metal.
- Direct Metal Laser Sintering (DMLS), where the metal powder is composed of materials with variable melting points that fuse on a molecular level at elevated temperatures.
- SMLS produces parts in alloys.
The key advantage of 3D printing is that it allows for complex shapes that are impossible with traditional forging methods. This can drastically reduce the number of parts in a machine that require assembly. It can also allow new innovative designs that are stronger or use less material.

Source: Hubs
Metal 3D Printing Evolution
More recently, new methods are being developed, for example Liquid Metal Printing (LMP) by MIT researchers. This method essentially merges together old-school free-form-casting with 3D printing.
This could remove the main limitation of metal 3D printing, which is that it tends to scale less well than traditional forging methods. While still keeping the advantages, like more complex possible shapes.
Overall, metal 3D printing is likely to keep growing, as it progressively demonstrates it can be as solid as forged parts while being price competitive thanks to less assembling and more efficient designs. This should consolidate metal 3D printing’s lead as the industry’s main market, currently standing at 53% of the total.

Source: Market.us
3D Printing Composite & Hybrid Materials
3D printing can also be done with mixes of materials. As we can see, this can be mixed with metals in alloys or different plastics. However, it can also be done with mixes of different materials.
One such example is composites, which mixes the 3D printed plastic with fibers. The additional fiber in the plastic increases the stiffness and strength of the produced part.
Most commonly, it is carbon fiber, but it can be fiberglass or kevlar.
Another option is hybrid materials, mixing 3D-printed plastic with something else entirely. You can, for example, have filaments containing organic material like bamboo, cork, or wood. Alumide, made of polyamides and aluminum powder, is another example of merging plastic and metal 3D printing together.

Source: BitFab
The combination of different materials is a growing trend in the industry, including the recent emergence of freeform multi-material assembly process (FMAP) that uses together fused filament fabrication (FFF), direct ink writing (DIW), and freeform laser induction (FLI).
Growing Applications
Aerospace
One key feature of 3D-printed components is that they can leverage their more complex shapes to reduce the amount of required material for the same structural integrity, reducing total weight.
This is a very attractive proposition for the aerospace industry, with every reduced gram allowing for better performance or larger payload, be it satellites to orbit or missiles on a fighter jet.
This is notably the advantage that is pursued by a company like Relativity Space, looking to create a 3D printed rocket, the Terran-R reusable rocket.
In-Situ Manufacturing
Sending anything into space is expensive, as in thousands of dollars per kilo expensive. This is a problem for any long-term presence in space, as it implies that spare parts need to be sent in advance and quantity just in case something breaks.
This, in turn, increases the budget for potential moon bases or Mars colonization by an order of magnitude. Such costs would be a dead end if we ever want to see the dawn of a space-based economy, including one that could provide an unlimited supply of green energy to Earth.
An alternative would be producing things on-site, ideally using locally mined materials like carbon and metals. While the idea is not new, the need to move entire forging stations into space made it unrealistic. 3D printers could help here.
They are much more compact than traditional manufacturing methods. With a limited stockpile of raw materials, they can manufacture thousands of different parts, only when they are needed. This would dramatically reduce the amount of unused “dead weight” in any deep space mission.
It is not anymore just an idea, with a 180kg prototype metal 3D printer by the ESA tested successfully in orbit in 2024.
Another prototype, the SpaceCAL, managed to print in a weightless environment more than 60 different materials, including silicone, plastics, glass composites, biomaterials, etc.
So it is likely that the future of space exploration will be based on reusable rockets, 3D printers, and local resources mined from the Moon, Mars, or asteroids.
Healthcare
Besides industrial prototypes and parts, a large revenue driver of the maturing additive manufacturing industry is the medical segment.
This is because, by their very nature, medical implants like dental or hip replacements need to be custom-designed for each patient. This is a key factor in keeping these treatments expensive, as there is no possibility of mass manufacturing an identical part for everyone.
This includes implants for the ear or mouth/teeth, but also 3D printed replacement “parts” for cancer patients or after a trauma like a jaw, rib cage, or part of the skull.

Source: 3D Natives
We also recently saw the first 3D-printed silicon heart valves, customized microporous bones, breast implants, etc.

Source: 3D Natives
Another role 3D printing could play in healthcare is in creating new forms of diagnostics and analysis.
For example, “organ-on-a-chip” & “body-on-a-chip” are now used to simulate a real body, in order to reduce the failure rate of clinical trials.

Source: Harvard
Another possibility is 3D printed drugs, allowing for more personalized healthcare, combining drugs, and reducing supply chain issues.
Bio-Printing & Soft robotics
The next step could be that instead of 3D printing the replacement of bones and organs by parts manufactured with metal, ceramics, and silicon, we directly “print” with living cells to create fully functional tissues and organs.
This is the promise of bioprinting. We explored in detail in a previous article how it works and what companies could benefit the most from it.
This could extend beyond internal organs and even include the bioprinting of brains, with already small cerebral organoids used by researchers on Alzheimer’s to study how brain tissues react to potential treatment. In the same way, neurons can be “printed” to create an artificial retina:
3D printing could also be used to generalize the field of “soft robotics”, by allowing machines to imitate biology (biomimetics). This could create safer and more functional robotic systems.
Semiconductors & Computing
Metal 3D printing can be done for implants or reactor jet parts, but it can also be done at a much smaller scale.
This opened the way to 3D printing with conductive or dielectric inks & ceramics. One leader of this technology is Nano Dimension, now also the owner of the metal 3D printing company Desktop Metal.
Nano Dimensions claims it can reduce the ecological footprint of manufacturing, with a reduction of 94% in CO2 emissions, 100% in water, 98% in materials, and 82% in chemicals.
Further progress is to be expected in 3D printed electronics, notably with the recent publication by researchers of flexible memory through “Liquid Metal Memory”.
3D Printing Concrete
Instead of going smaller, additive manufacturing can also go bigger. A lot bigger when it comes to 3D printing entire houses and large buildings. For example, the first-ever 3D-printed mosque opened in 2024 in Saudi Arabia.
As you can imagine, the scale of the nozzle and the 3D printer is off the chart when it comes to such a project.

Source: Cornell University
3D-printed buildings require a lot less labor and could come out significantly cheaper, as we discussed in our article “Home Ownership is More Prohibitive than Ever Before in North America – Can 3D Printing Change This?”
This new method for construction could have applications beyond Earth:
The company ICON has been selected by NASA for Project Olympus, a $57.2M contract for a 3D printing system to create on the Moon landing pads, roadways, non-pressurized structures, and pressurized habitats, using local regolith (Moondust) instead of imported from Earth materials. The same method could be used for Martian habitats as well.

Source: ICON
The Future Of Additive Manufacturing
Improving Technology
Traditional manufacturing has gradually improved over the more than two centuries of the Industrial Revolution, or even longer when it comes to metallurgy.
So, it is perhaps not surprising that 3D printing is still only starting to realize its full potential.
Problem Detection
For example, metal parts for the aerospace industry often need to be X-rayed to determine if the printing worked properly without defects. This is both expensive and slows down production. Instead, researchers found that AI deep learning combined with CT scans can work.
Meanwhile, a technique called acoustic monitoring (detecting through sound a problem) could help detect defects in real-time.
New Production Methods
Among potential improvements, we could replace the currently used two-photon polymerization (TPP), requiring dual femtosecond laser for micron-scale industrial prints. As TPP is expensive, the discovery that lower-power lasers could perform equally well could grow the market further for 3D printing of microelectronics.
So far, almost all methods rely on using a solid (filament) or a powder and then melting it. However, new 3D printing ideas are still emerging, notably vapor-induced phase-separation 3D printing (VIPS-3D). This method could be very powerful for complex part mixing material or requiring variable levels of porosity. It would also require a lot less materials and less power, reducing costs.
4th Industrial Revolution & Decentralized Manufacturing
3D printing has, for a long time, been the reserved domain of industrial experts and passionate hobbyists. It also required a significant upfront investment, with the risk of the acquired machines being too many or too few compared to real needs, leading to capital inefficiency.
This is less and less true, thanks to large service providers offering the usage of 3D printers as well as skilled labor as a service. This pools together the resources of many different users, smoothing the peak in demand for the 3D printers.
These providers often combine the 3D printing services with CNC machining (Computer Numerical Control), 3D scanning, 3D design, etc.
The rented machine could even be accessed directly by the user through the cloud in some cases.
Meanwhile, researchers in various fields like biology or chemistry are discovering that you might sometimes replace a $100,000 part in a mass spectrometer with a part 3D printed directly in the lab costing only a few dollars.
Overall, we are likely to see a growing flexibility of the supply chain, as well as more delocalized manufacturing emerging from the generalization of 3D printing.
This will make additive manufacturing a key component of the ongoing 4th industrial revolution, together with AI, robotics, smart factories, connectivity, IoT, etc.
Investing In 3D Printing
3D printing is only now reaching technological maturity, as well as market consolidation. This gives investors a little more visibility than in the past and confirms that this technology is far from a fad but is here to stay.
You can invest in 3D-printing-related companies through many brokers, and you can find on this website our recommendations for the best brokers in the USA, Canada, Australia, the UK, as well as many other countries.
Besides the companies discussed below, you can also find potential investing ideas in our article “Top 10 Nanotechnology Stocks”.
If you are not interested in picking specific 3D printing companies, you can also look into ETFs like ARK Invest 3D Printing ETF (PRNT) to capitalize on the growth of the additive manufacturing sector as a whole.
3D Printing Companies
(Besides the companies discussed below, you can read about others in our article “Top 10 Additive Manufacturing And 3D Printing Stock to Watch”)
1. Nano Dimension
Most additive manufacturing companies focus on metal and plastic, with an eye for complex mechanical parts. Nano Dimension is instead focused on 3D-printed electronics. This includes very specialized technologies like conductive or dielectric inks & ceramics. These can for example be used for building optical or radio components.
This is one of the possible applications of 3D printing to the nanoscale, which we explored further in “Nanoscale 3D Printing Looks Primed for Commercialization”.
Nano Dimension has grown through a mix of acquisitions and internal R&D.

Source: Nano Dimensions
This strategy reaches a new high with the acquisition of Desktop Metal in 2024. Together, the 2 companies will have a much stronger position in metal and ceramics 3D printing at all scales, from electronics to large industrial equipment and aerospace.
This also creates economies of scale by merging the customer base that includes SpaceX, Tesla, GE, Honeywell, Emerson, Raytheon, NASA, Medtronics, etc.
Lastly, the two companies were mostly active in different geographic areas, with Nano Dimension in Europe and Desktop Metal in the US, allowing for synergy by merging their sales teams.

Source: Nano Dimension
The company claims it can reduce the ecological footprint of manufacturing, with a reduction of 94% in CO2 emissions, 100% in water, 98% in materials, and 82% in chemicals.
Overall, we can expect Nano Dimension to emerge as one of the technology’s leaders.

Source: Nano Dimensions
However, investors need to be aware that both per-acquisition Nano Dimension and Desktop Metal were cash flow negative, so the resulting company will need to cut costs or grow sufficiently to turn a profit in the future.
2. 3D Systems Corporation
3D Systems can print 130 materials, producing over a million parts daily. In Q4 2023, it delivers 5 new materials and 3 printer upgrades.
In 2023, revenues declined slightly, due to a contraction in orthodontics and dental segments, driven by reduced consumer spending. It was partially compensated by strong growth in the aerospace, jewelry, and other segments.
It is also working on a 3D bioprinting technology, which could be used to create synthetic organs, with a target for 2026 for the human trial in lung transplant. The addressable market is estimated at $4B.
The company keeps making progress in that field, notably with the most complex object ever 3D printed (a human lung scaffold) and organ-on-a-chip through its fully-owned subsidiary Systemic Bio (contract with 2 of the top 4 largest pharmaceutical companies).

Source: 3D Systems
Past (and Future?) Mergers
The 2023 tentative for a merger with Stratasys was rejected by its shareholders. It is however yet to be seen if the recent merger of Nano Dimension and Desktop Metal creates some urgency for its competitors to merge into an even larger company.
If no more mergers among the largest 3D printing companies occur, it is likely that the industry will drift toward an oligopoly of 3 companies: 3D Systems, Stratasys, and Nano Dimension, with smaller actors like Velo3D and Markforged forced to either merge with each other or be absorbed by one of the “big 3”.